Process Innovation Explained: Definition, Benefits & Examples
Jul 24, 2024 • 10 min read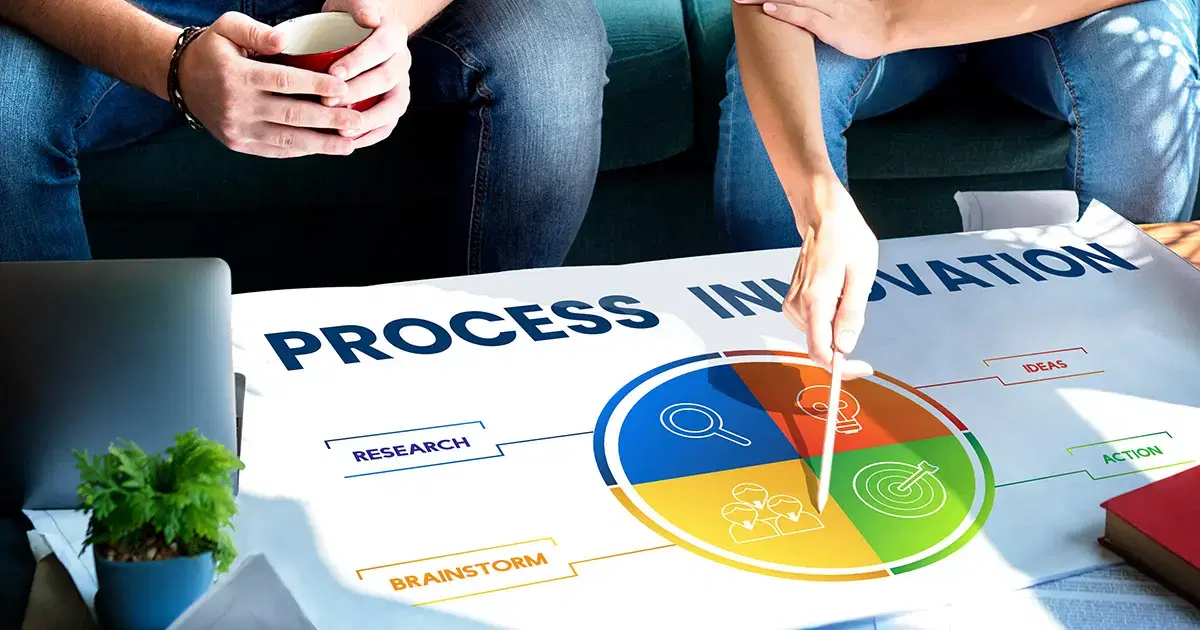
What is Process Innovation?
Process Innovation is defined as a process that delivers more value to customers or optimizes a company's operations. This is usually done by introducing changes to existing processes or building and implementing new ones.
Unlike product innovation, process innovation may remain invisible to customers. This is mainly because it might relate to production or delivery processes that customers cannot observe. Product innovation usually brings value through new functionalities and integrations, while the benefits from process innovation might be less visible, like higher quality products, faster production, cheaper cost of goods, etc.
Process innovation is very connected with incremental innovation as both concepts are based on the same method of observing, hypothesizing, and testing. Some process innovations made on existing processes might be considered incremental innovations. However, it’s important to note that process innovation might be a completely new process that won’t be considered incremental.
What are the 5 steps to Process Innovation?
Now that we understand process innovation, let’s see how to create it.
1. Observe
It’s next to impossible to improve anything that you can’t observe. Some processes are well documented, which provides enough touchpoints to observe their performance. For example, the customer support process in a SaaS platform usually involves a helpdesk system, and the whole customer journey can be followed.
In other cases, the business processes might be less explicit and observable. Consider the manager's yearly evaluation of employees, which is done in a 1:1 conversation without a documented trail.
When improving a process, your first objective is to ensure it can be studied.
2. Measure
As a next step, it is important to define what success looks like for the desired improvement and pick a way to measure it. In addition to a success metric, multiple leading indicators, such as KPIs, might be useful to reduce feedback time.
For example, if we want to reduce the quantity of scrapped items at the end of the production process, adding multiple checkpoints through the manufacturing process could be valuable indicators of whether the suggested changes produce results.
3. Analyze
The third step in process innovation is to identify areas of improvement. This can be done in both the current process or the characteristics of how the improved process would look.
Depending on the success metrics, we might be looking for different things:
- A bottleneck in the process - this would be helpful if you are aiming to increase production capacity
- Hotspots of defects - this can be a useful metric if the goal is to increase the quality
- The biggest cost drivers - this can be a good indicator if you are looking for ways to reduce cost
4. Hypothesize
After identifying the most problematic area, build a list with hypotheses, including the changes you think would drive the needed positive impact. The hypothesis should consist of:
- The change that will be introduced,
- The outcome that is expected,
- A measurement to prove the outcome is present.
Example:
By introducing a chatbot as a first-level support officer in the customer support process, the number of support requests handled by the support team will be reduced by 20% without negatively impacting customer satisfaction.
Let’s dissect this hypothesis into its key components:
- The change: introduce a chatbot into the customer support process as a first–level support
- The outcome: reduce the amount of requests handled by the support team
- The measurement: 20% reduction in the requests without negatively impacting customer satisfaction
The Icanpreneur platform provides a structured approach for defining and validating your customer hypotheses.
5. Test
The final stage of the process would be to implement the suggested change and test it. The tests might be done without a full-blown implementation to reduce the experimental costs and increase the learning rate.
Sometimes, a mock of the process or a stripped version might be more than enough to prove the point. This can be extremely useful when you want to test specific use cases.
After the test is conducted, you should assess its success based on predefined success criteria. This will help you decide whether you want to make changes to the hypothesis and repeat the test or if you are happy with the result and will proceed with implementing a long-term solution based on the experiment's results.
4 Key Benefits of Process Innovation
1. Better Products
Process innovation can be focused on addressing underserved customer needs leading to new or improved products.
2. Speed and Time Savings
Some process innovations target customers' needs indirectly by cutting down lead time or cycle times (see the example below with NVidia). This can lead to better customer service, boosting the learning cycle and making the company more competitive due to its nimbleness.
3. Operational Excellence
By implementing process innovations, a company continuously improves its operations. This leads to high profit margins, better customer service, and reduced operation costs.
4. Competitive Advantage
Innovative processes often lead to better performance than competitors. If the process innovation relies on external expertise or resources that are not widely available, it can turn into an unfair advantage. Such innovations are incredibly valuable for the valuation of the company during fundraising or acquisitions.
Real-life Examples of Process Innovation
NVidia
Did you know that after their first unsuccessful attempt to create a graphics card, NVidia (now a trillion-dollar company) was just nine months away from bankruptcy? The process of creating a new chip—from design, testing, and approval to final market production—would take two years. At the same time, the company had only nine months of runaway.
To survive, the NVidia team used a software simulator during the design process. This simulator was incredibly slow, producing one frame every 30 seconds. However, sending the foundry ready-for-production requirements saved them more than 60% of the production time.
Later, this situation led to a significant competitive advantage for NVidia. It allowed them to have a radically faster release cycle in a market where go-to-market time means everything. The unique supply chain they created is a hard-to-replicate advantage.
Toyota
Toyota’s process innovation transformed the company into one of the most efficient car manufacturers globally. It also influenced manufacturing practices across various industries, leading to the widespread adoption of lean principles.
The Toyota production system (TPS) introduced just-in-time production. These principles reduced the inventory that had to be managed, which in turn, led to cost and waste reduction. The TPS also pioneered the lean manufacturing principles, which are now transferred and widely adopted in the IT industry.
Amazon Kindle
Even if you haven’t published a book in your life, you probably have a good idea about what the book publishing process looks like. An author sends a book to a publisher, who sends it for editing, copywriting, translation, publishing, and distribution to retailers until it reaches readers.
Through its Kindle product, Amazon, cuts parts of that cycle by offering a digital book experience comparable to reading a physical book. However, the new process eliminated the need to produce physical copies of the book, distribute them, store them, etc.
This meant that a reader could buy a book that was published yesterday immediately all around the world without even visiting a bookstore. Amazon optimized its costs as the biggest retailer of books and delivered customer value by providing books faster, cheaper, and without having to store them in a physical library.
UPS
Logistics operations often involve complicated processes due to the multiple stakeholders involved and the uncertainty that can change the course of action. The UPS Package Flow Technology optimized the delivery routes and improved package tracking, reducing fuel consumption, increasing customer satisfaction, and improving efficiency.
This was achieved thanks to:
- The introduction of RFID tags for tracing the packages,
- Building a better algorithm for route planning,
- Installing automated sorting systems.
Tesla
With the introduction of over-the-air updates, Tesla reinvented the process of updating the functionalities of their cars, borrowing the concept from smartphones, laptops, and smart TVs.
By streamlining the updates process, Tesla achieved the following optimizations:
- reduced the need to visit the service,
- reduced the time it takes the deliver value to customers through updates,
- provided infrastructure for continuous innovation that creates a continuous stream of improvements.
This innovation facilitates more than just the car manufacturer's regular operations. During Hurricane Irma, Tesla unlocked additional capacity in the car batteries with an over-the-air update to ease the evacuation process for Tesla customers.
This was possible thanks to another innovation in their process—all cars, regardless of their range, were equipped with the same battery, which was limited through software for small-range vehicles. This helped them streamline the car production process.
Top 5 Best Practices for Process Innovation
1. Focus on Customer Value
Understanding customer needs and problems is the first step to identifying pain points in your processes. The Icanpreneur platform navigates entrepreneurs and product leaders through conducting customer problem interviews, ensuring that insights and conclusions from the interviews are unbiased and confident.
2. Document the Process
We often think of processes as well-documented and structured sequences of activities that deliver consistent results.
However, many processes are informal, inexplicit, and can provide sporadic results. A process has to be well understood and analyzed, if you aim to improve it. Before attempting any improvements, the process must be described in diagrams or bullet points.
3. Associate a Process Change with Clear Business Outcomes
If you want to drive value, every improvement attempt must be aligned with the company's goals and objectives. The connection between the proposed change and the expected business outcome needs to be explicit and understood by all stakeholders in the process.
4. Empower and Engage Employees
As the saying goes:
Culture eats strategy for breakfast.
Make sure that employees’ incentives are aligned with the process innovation being introduced to avoid boycotting. Changes are hard, and introducing a change needs to account for that and have an appropriate change management plan.
5. Automation
Automating parts of a process is one of the most impactful types of process innovation as it usually brings all the benefits: reduced cost of operation, increased quality, better products and services, etc.
Automation started with the Industrial Revolution when machines replaced manual labor. Now, we are on the verge of the AI revolution, when computers can replace operations previously executed by knowledge workers.
Wrap Up
Process Innovation is a strong component of embracing the continuous improvement philosophy in your organization. It can be a bearer of incremental improvements but can also unlock discontinuous innovation and disruption of existing markets.
Follow the Icanprener LinkedIn page to learn more about the different innovation types or access real-world examples and guidance from experts.
Author

Product @ Icanpreneur. Coursera instructor, Guest Lecturer @ Product School and Telerik Academy. Angel Investor. Product manager with deep experience in building innovative products from zero to millions of users.